Verity Construction Verification Software Reduces QA Time from One Week to Six Hours per Floor
For a recent high-rise renovation project, Rogers-O’Brien implemented a same-day QA process built on ClearEdge3D’s Verity. It enabled RO to find and fix errors in the structural concrete with unprecedented speed — minimizing schedule delays and greatly reducing unexpected rework costs.
The Project
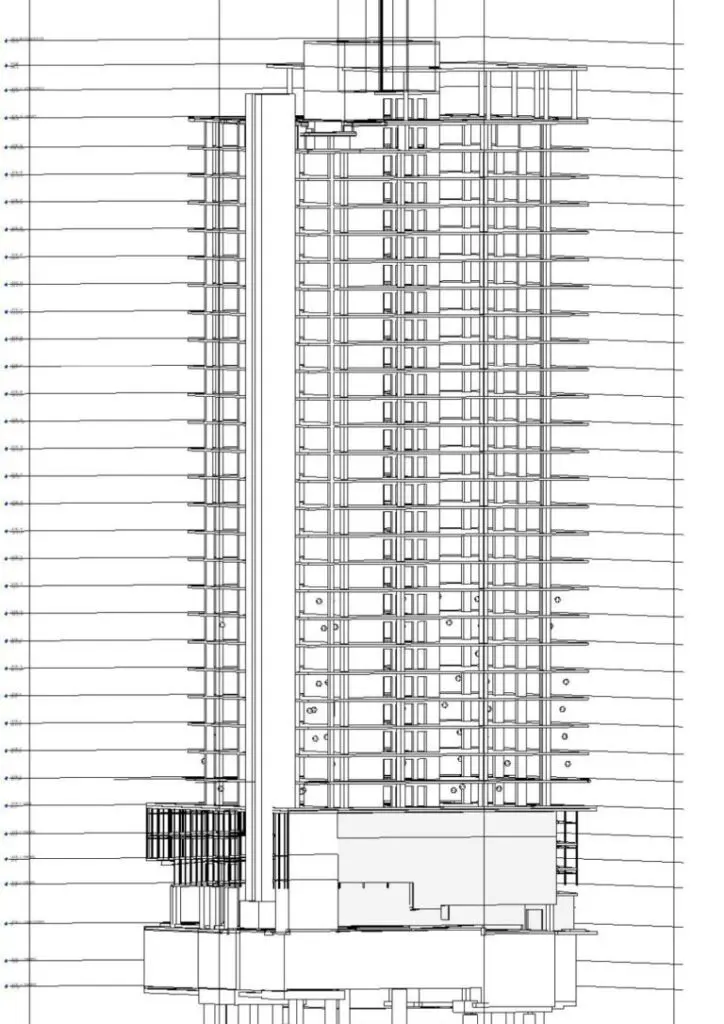
Rogers-O’Brien’s comprehensive Revit documentation of the high-rise in Austin, Texas.
A commercial high-rise remodel
Last year, Texas-based general contractor Rogers-O’Brien renovated a high-rise project in Austin, Texas. RO was responsible for 27 residential floors, each 14,000 square feet in area, for a total of 380,000 square feet.
The Challenge
Ensuring precise installation is critical to maintaining project schedules and controlling costs
Like many fast-paced construction projects, this high-rise renovation required a keen focus on quality control to mitigate risks before they escalated. With the rapid pace of construction, RO was prepared to leverage advanced technology to catch potential issues before they could impact the schedule. “By identifying and addressing potential discrepancies early, we can prevent any ripple effects that might affect the project timeline,” says Michael Clark, RO’s director of field engineering.
“Think about structural concrete,” he says. “If a deck or slab edge is off by just an inch or two, we wouldn’t realistically know about that until another trade tells us. Maybe the glazers are
coming out to install window points and they find the error two weeks after installation. Then we might need to spend a month-and-a-half fixing the problem before they can return to work.”
Impeding one trade affects the rest of the critical path. Delay the glazers, and you delay the installation of MEP, HVAC, the building’s skin, and so on. Every error pushes the delivery date further out, potentially costing the GC tens of thousands of dollars in unnecessary field hours.
And that’s not even accounting for liquidated damages, which are contractual fees the owner can charge the GC for every day or week the project goes over schedule.
RO is committed to avoiding pitfalls seen throughout the industry by implementing proactive solutions. They recognize that with careful monitoring, they can prevent installation issues and escalating project costs.
Optimizing QA Solutions
Previous QA/QC workflows were too slow for the fast pace of construction
Rogers-O’Brien understood that the traditional manual QA workflows could not keep up with the demanding pace of their projects. Errors needed to be caught and corrected quickly, but the manual processes were far too time-consuming, labor-intensive, and reactive.
The company explored using a lidar-based QA workflow to speed up error detection and correction, which involved manually comparing as-built point cloud data with the design model. However, they found that even this approach was inefficient.
“It was too time-consuming to scan and review the data,” says Michael Clark, RO’s director of field engineering. “Even with the newest scanners, you still need someone to compare the point cloud against the Revit model manually. It just isn’t feasible. Work progresses too quickly, and there’s too much else to do.”
RO has continuously explored cutting-edge QA technologies to increase efficiency and accuracy. While valuable, they saw the potential for further improvement, which led them to explore solutions that would keep up with the fast-paced nature of modern construction and improve real-time decision-making.
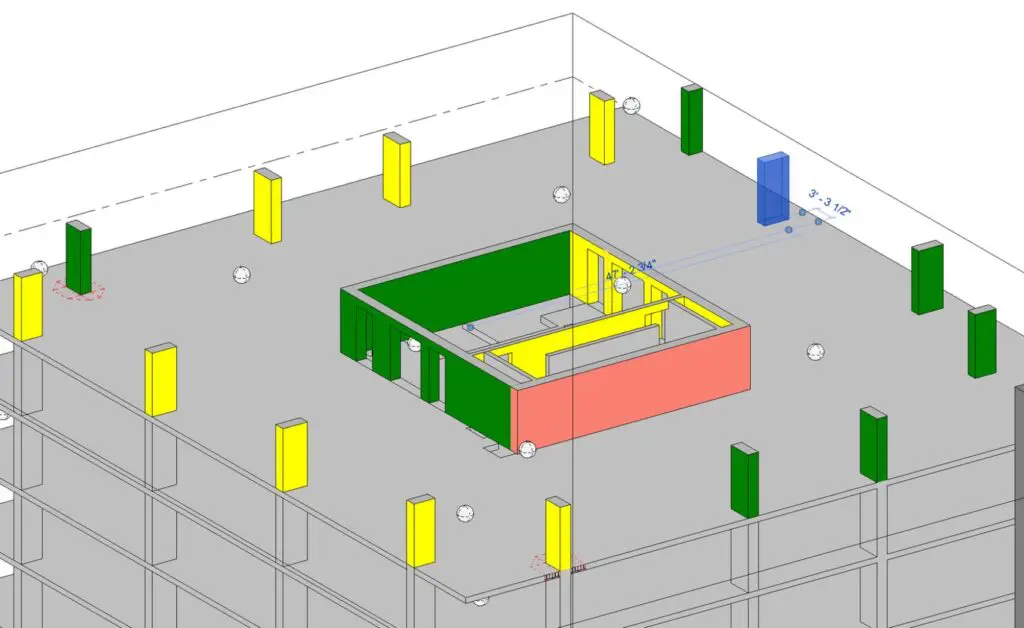
A Revit model of the high-rise’s structural concrete colorized based on Verity analysis results to display deviation between the design and as-built conditions.
The Verity QA workflow
RO found faster, more effective QA with Verity, GTL-1200, and Collage Site
On the high-rise renovation project in Austin, RO found their ideal solution, using ClearEdge3D technology to build a verification workflow for structural concrete.
The reality capture team used the Topcon GTL-1200 to capture point cloud data one floor at a time. This tool combines a robotic total station with a lidar scanner so RO can set survey control and scan simultaneously with a single device.
On each floor, the team captured ten scans, four with survey control and six without. As they scanned, they registered the point cloud with Collage Site. By the time scanning in the field was complete, the team had a single, structured point cloud tied survey control.
Now, they used ClearEdge3D’s Verity for analysis. Verity is an as-built verification tool that integrates with Revit and Navisworks to process point cloud data and identify deviations from design and coordination models automatically.
Since RO uses a shared coordinate system between Revit and the field, loading the point cloud into Revit took only a few minutes. Then, it was as simple as isolating the structural concrete columns and walls, running a Verity analysis, and producing reports and visualizations that made it simple to review variances and check for issues, and do it before the project moved on.
Other benefits
Faster analysis, better communication
Verity wasn’t just a fast and effective tool for QA’ing structural concrete. It was also remarkably easy to use. Clark says the software’s interface is so intuitive that he can perform analysis and generate reports within 30 minutes.
Verity streamlines the analysis process, enabling RO’s teams to achieve even higher standards in a fraction of the time. It produces highly visual, intuitive documentation that delivers faster and more accurate results, accessible to both specialists and non-specialists alike.
Verity has improved communication with project teams. “They’re very visual people,” he says. “They don’t like a report with just a bunch of numbers like we used to get out of our old QA workflow. It was difficult for them to visualize where an element was off, or how it was off.”
With Verity, Clark can run a fast analysis and then open Revit to walk the project teams through the model. “I just show them where an element is supposed to be and where it was actually installed. It’s simple.”